The unexpected failure of a hospital’s two boiler feed pumps left them with only one operational pump and a critical need for a replacement. However, long lead times put them in a precarious position and a creative solution needed to be found. Fortunately, the Geiger team of engineers leveraged their technical know-how and in-stock inventory to configure an effective drop-in replacement to maintain the hospital’s operations while they waited for the new replacement pumps to arrive.
The Problem: Multiple Boiler Feed Pump Failures
A hospital had three boiler feed pumps that had been in service for over 20 years. Two of the pumps had developed leaks at the attachment point of the flanges to the pump casing, forcing them to be taken out of service. Failure of the remaining pump would mean the hospital would no longer have heat or hot water, so they were urgently trying to source replacement pumps.
The original model of pump was not known, and the group of pumps had become obsolete, replaced with more efficient pumps. They needed a drop-in replacement that would provide the same flow and head as the original pumps, but only the motor nameplate was legible. Additionally, because of supply chain disruptions, the lead time for all similar pumps was running 25 weeks – far too long to wait.
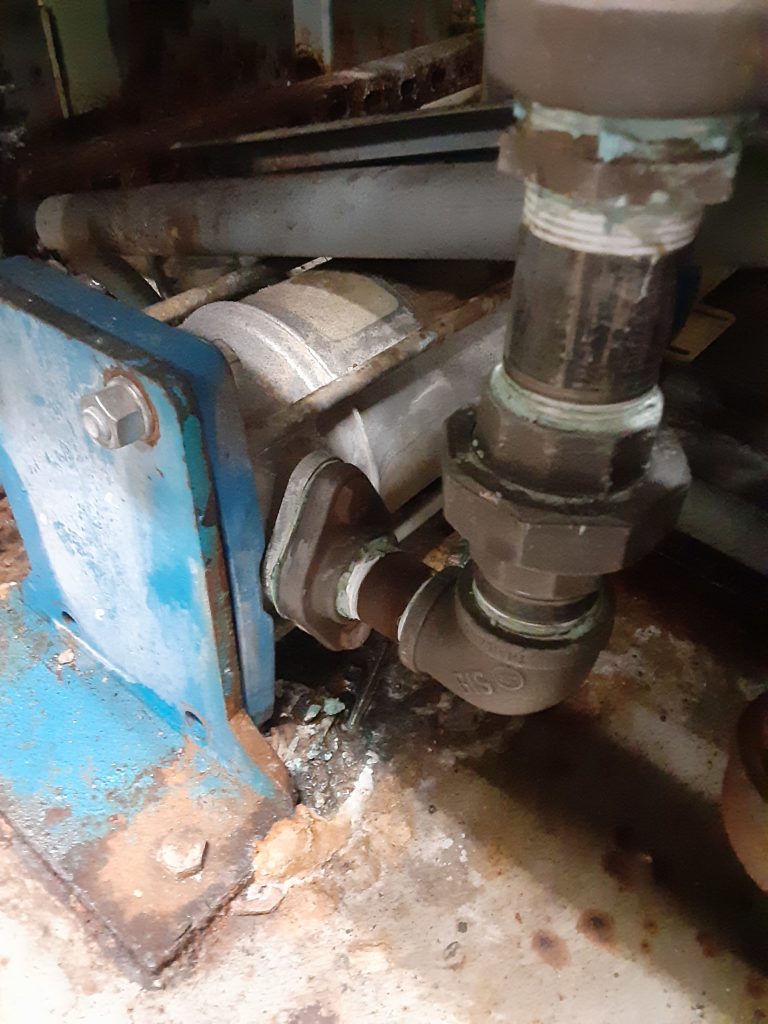
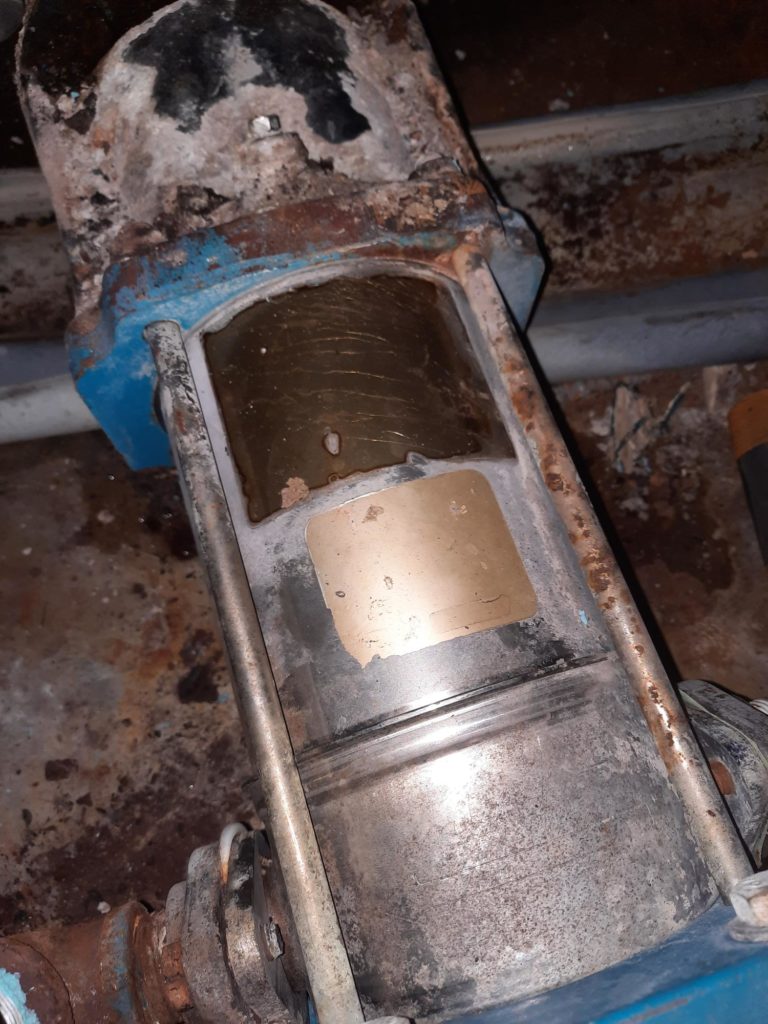
The Solution: Pump Assembly Using In-Stock Parts
Once realizing the lead time would be too long to wait for a solution, Geiger’s team evaluated one of the old pumps that was no longer in service and was able to positively identify the obsolete model and the currently available replacement from within Xylem’s Goulds Water Technology e-SV line of pumps. However, the lead time was still quite long, and because of the hundreds of combinations of pump available in this line, Geiger did not have the exact model in stock. However, because of our strategic stocking, our experienced team was able to evaluate pumps in stock and determined that we could dismantle two liquid ends and reassemble them into a single pump that could be used as a drop-in replacement.
The Results: Immediately Mitigated The Risk Of Downtime
Geiger’s creative problem-solving resulted in an operational drop-in replacement installed within a few days instead of months. The resulting pump was placed into service and performed effectively, giving the hospital time to get their additional replacement pump and shelf-spare without worrying that they would be without the critical service of these pumps.
To learn more about Geiger’s capabilities or in-stock inventory, contact our team.