If you operate or maintain pumps, mixers, blowers, agitators, or any of a wide variety of other rotating equipment, you know how critical it is to have a reliable shaft seal and how troublesome an unreliable shaft seal can be. Mechanical seals are the most used type of engineered seals, ranging on from small, inexpensive component seals, to highly sophisticated, engineered devices used on the most demanding applications. Read on to learn about the basic types of mechanical seals, and how Geiger’s team can help you choose the right seal for your application or troubleshoot and upgrade existing seals.
How Does A Pump Mechanical Seal Work?
Mechanical seals are a shaft sealing technology that use two finely machined, smooth faces running in contact to seal around a rotating shaft. One seal face is sealed with an elastomer to the shaft and rotates with the shaft, and the other face is sealed to the equipment casing or seal gland, and is held stationary. The seal faces are pushed together so they rotate against each other, lubricated, most commonly, by the process fluid, preventing process fluid from leaking around the shaft. Depending on the application, mechanical seals may be spring or bellows loaded, single or double seals, balanced or unbalanced, or pusher seals. Mechanical seals may be stand-alone devices or may need flushing water, cooling, or other support systems.
Looking for API 672 seal plans? Check out the reference guide here.
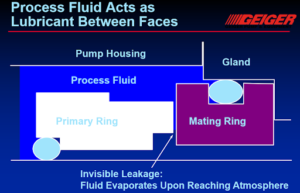
Cartridge vs Component Seal: How Do I Choose?
Mechanical Seals can be purchased as separate components which must be separately installed and properly compressed by a skilled technician. Cartridge seals provide all the components of the seal assembly as a factory assembled, properly compressed, and aligned unit which can be easily and quickly installed. The parts for component seals are less expensive than a cartridge seal, however in most cases when labor and availability of skilled technicians is considered, cartridge seals are a better value.
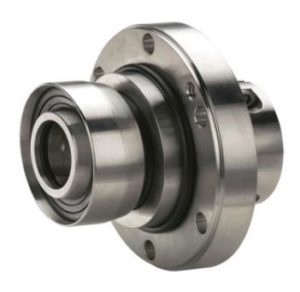
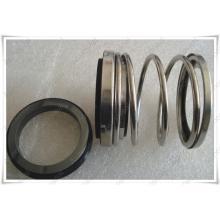
How Long Do Mechanical Seals Last?
It really depends on the application. Some seals may last years. Other seals, in more demanding applications such as abrasive or high temperature service or on aggressive chemicals, may need much more frequent replacement. Note that mechanical seals are considered a normal wear component, however there are often ways to extend the time between maintenance or failure.
If you have a seal that frequently needs replacement, contact us or discuss the application with your sales engineer. Geiger Provides:
- Seal Failure Analysis
- Alternate sealing solutions such as face material upgrades or adding a seal support plan, or moving to innovative O-Pro or seal-less technologies
- Strategies and products to make replacement easier, such as converting component seals to cartridge seal or converting large diameter shafts to split seals
- Cost Saving Seal Repair
Did you know many seals can be renewed to return them to new condition?
Many styles of seals can have their faces re-lapped and elastomers renewed to return the seal to like-new condition. When replacing a larger seal, be sure to ask if the old seal can be repaired so you’re never without a spare.
How To Choose The Correct Mechanical Seal For Your Pump or Other Rotating Equipment?
When selecting a pump, blower, mixer, or vacuum pump for your application, the application engineer will also select a coordinating seal which will come installed with the equipment. Seals can also be purchased separately for repair or replacement, or to upgrade an existing shaft seal. When selecting a seal, our application engineers will consider the style of seal for the application and equipment, seal face material, compatible elastomers, and additional seal support systems needed such as flushing or cooling.
Application details needed for seal selection include:
- Process Fluid Name (and if applicable, Concentration)
- Process Temperature
- Viscosity
- Process Fluid Pressure
- Solids Content/Abrasives
- Environmental Regulations
- Shaft Size
- Equipment Type (Blower, Mixer, Pump, etc)
Contact our engineering team for assistance with seal selection for your particular application
Other Shaft Sealing Options:
- Seal-less Pumps: Magnetically driven pumps offer complete containment without the need for any seal. Geiger offers centrifugal and positive displacement, magnetically driven seal-less pumps including ITT Goulds 3298, Viking Pumps’ CMD, Moyno mag drive pumps, and more.
- O-Pro: Viking Pumps’ groundbreaking O-Pro seals are a highly effective replacement for packing in traditionally challenging sealing applications such as chocolate and asphalt.
- Packing: Traditional shaft packing is easily installed, inexpensive, and still a good solution for many applications, especially high viscosity fluids.
- Lip Seals: From basic lip seals to triple lip seals allowing API sealing plans, physically compact lip seals are problem solvers when properly applied.
View our full line of pumps and mechanical seals.