A cogeneration power plant in New Jersey approached our company with an urgent need for a large vertical turbine pump repair to be completed during their scheduled shutdown. As a trusted service provider, they requested our on-site support as a general contractor to ensure a seamless turnaround process. The plant faced significant pressure to restart operations promptly, making it a critical project demanding the collective effort of our entire team.
The Problem: Time-Sensitive Repair Of A Large Vertical Turbine Pump
The project involved the repair of a large vertical turbine pump with a 20-inch discharge and spanning 15 feet in length. Our team swiftly responded to the client’s request, led by our capable senior Field Service Technician. We secured a qualified subcontractor and coordinated and supervised multiple vendors and contractors to handle the specialized task at hand. Our team expertly managed the logistics and ensured the subcontractor possessed the necessary credentials to access the plant premises.
Unexpected Pump Deterioration
The pump, initially believed to have minimal issues, was carefully removed from the plant and transported to our facility. Our skilled millwright meticulously dismantled the equipment for a thorough inspection. However, upon closer examination, we made unexpected discoveries that revealed the full extent of the pump’s deterioration. Cracked impellers, destroyed cutlass rubber bearings, a worn pump shaft, a bent drive shaft, and a damaged head shaft presented significant repair challenges. Furthermore, the couplings exhibited severe galling, necessitating their replacement. The damaged shaft sleeve had to be carefully cut off, adding to the complexity of the repairs. What initially seemed like a straightforward task turned into a major restoration project under a tight deadline.
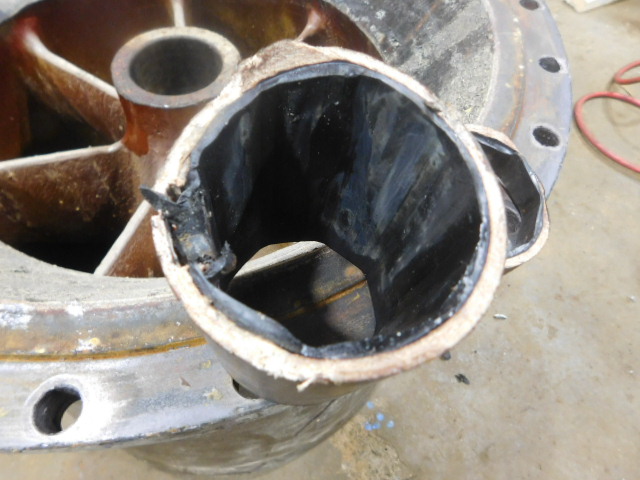
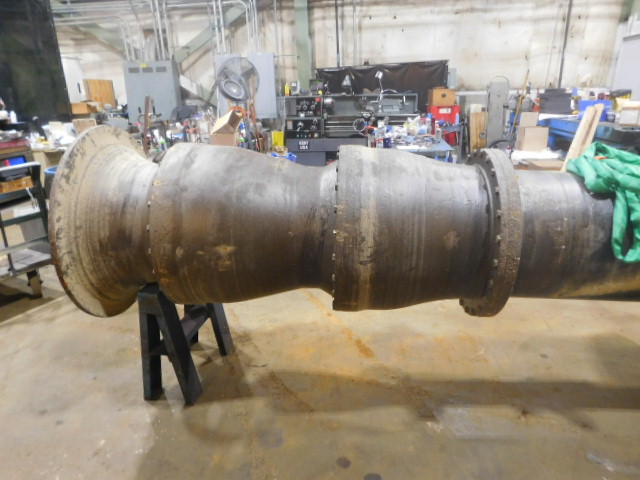
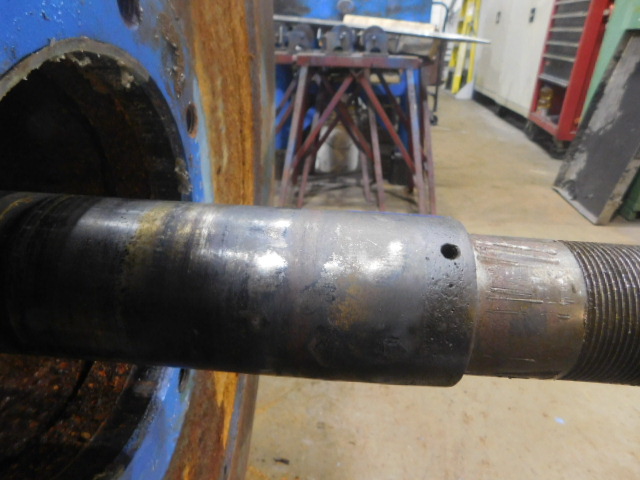
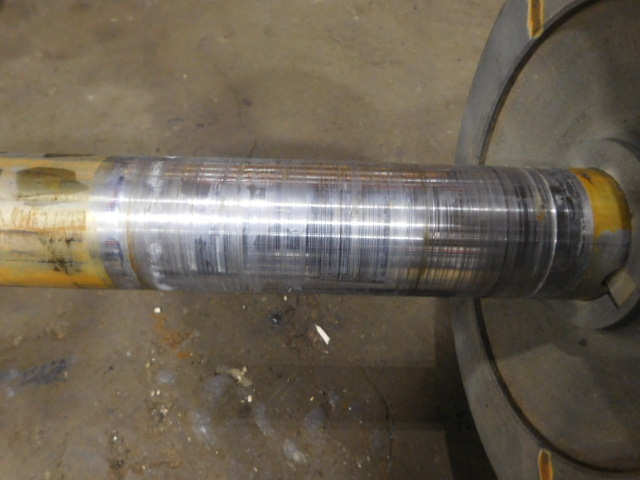
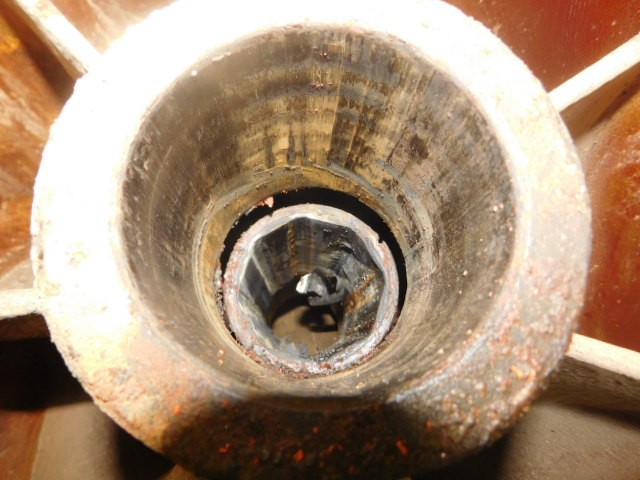
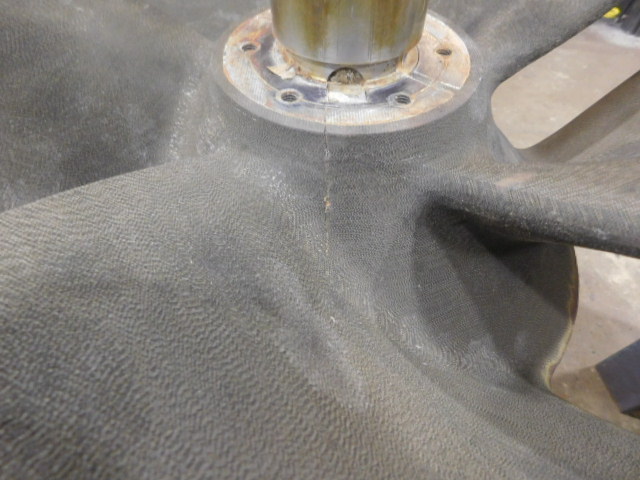
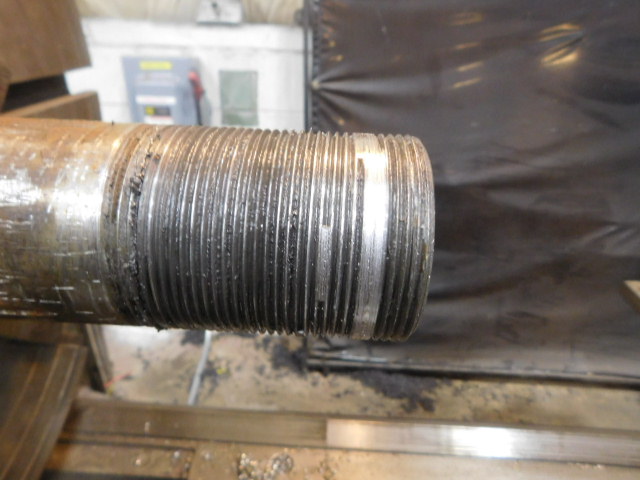
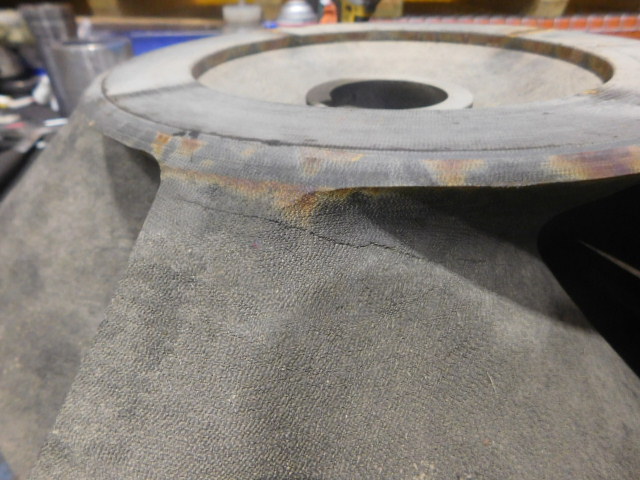
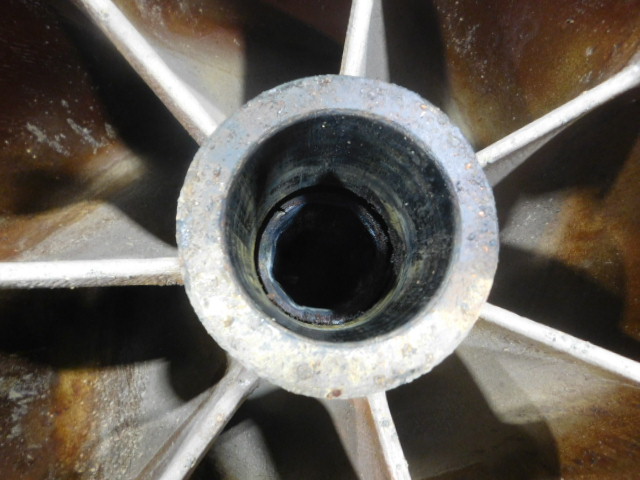
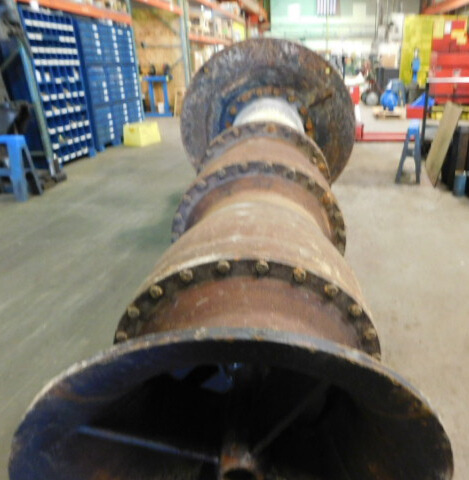
The Solution: Effective Parts Sourcing & Reassembly
The client expected to have adequate spare parts on site based on the original repair scope, however, once the extent of damage was revealed to be much more extensive it became apparent that not all the necessary components were available. Our Repair Coordinator promptly sprang into action, sourcing shafting, couplings, and miscellaneous hardware from reliable suppliers. Despite the time constraints and unusual materials, she managed to secure the required materials and ensured their delivery to our facility within an impressive three to four days. Such efficiency in parts acquisition greatly contributed to the overall project timeline.
Armed with the newly acquired components, our team embarked on the meticulous reassembly process. Our Millwright and Senior Field Technician led our work, making sure newer Technicians received invaluable hands-on experience while working under the guidance of our experienced team. Their collaborative efforts enabled the smooth execution of the repair and subsequent installation. The collective expertise and dedication demonstrated by the team were instrumental in overcoming the complexities encountered during the restoration process.
The Results: Finishing Touches and On-Time Completion
Following the successful reassembly we applied a fresh coat of paint to the pump. The end result was a visually appealing and fully restored piece of equipment. Despite the additional challenges encountered during the repair, we successfully completed the project within the required timeframe. The restored pump was promptly returned and installed at the plant, enabling the client to restart their operations as scheduled.
Key Takeaways and Acknowledgments
This case underscores the Geiger Pump and Equipment team’s ability to adapt and excel in demanding, changing projects. By leveraging the expertise of our team members, we effectively tackled the intricate repair demands of the vertical turbine pump. The successful collaboration and coordination between our staff members and the client’s team played a pivotal role in achieving the desired outcome. We extend our deepest appreciation to everyone involved in this project for their exceptional work, dedication, and commitment.