This guide is designed to help you understand some of the more common and complex Mechanical Shaft Seals technologies on the market. This guide addresses the following topics:
Prefer to watch to this content? View theses topic videos on our free Shaft Seal Training Series.
Packing for Mechanical Shaft Seals
Packing is the traditional way to seal around rotating shafts to prevent liquid from leaking . Packing has a long history as a sealing technique, and is one of the oldest technologies still on the market today.
What Is Packing?
Packing is a fibrous, braided material, cut and formed into rings inserted into a stuffing box, around a seal. Packing is typically combined with a Lantern ring in between rings for external lubrication, and is compressed by a packing gland to improve sealing. The types of materials that can be used for packing are vast, providing many options for application – and many opportunities for misapplication. Below are a few parameters your application engineer will need to choose the right packing for your application:
- Shaft speed
- Process liquid including pH and solid content
- Temperatures
- Pressures
How Is Packing Installed?
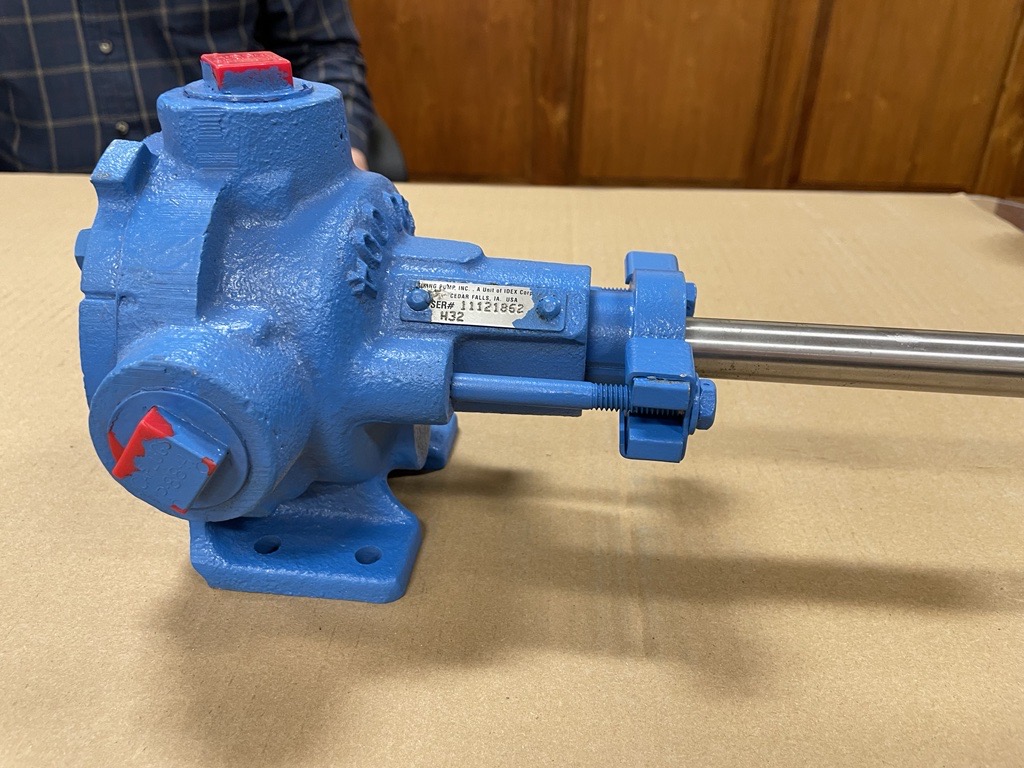
Packing is installed in a stuffing box of a pump. It is important to ensure that the stuffing box bore or the square all the way through the pump without any grooves, nicks or anything that would allow external leaking on the OD of the packing. Packing and the lantern ring are inserted around the shaft, staggering the cuts in each ring to reduce leakage. Finally the packing gland is installed and tightened to compress the packing. Note, over tightening packing can result in damage to the shaft. It is normal for packing to leak several drops per minute.
There are a few things to keep in mind during this process. If the shaft sleeve is worn, it is likely the packing will still leak excessively, even when tightened. Secondly, packing is used to control the amount of leakage to the atmosphere but all packing must also leak for it to operate properly. The key is to aim for a controlled amount of leakage probably 10 to 12 drops per minute per one inch of shaft size. Some leakage is needed to assure lubrication of the shaft at the packing.
Looking for a solution that doesn’t leak? Check out the O-pro seal, mechanical seals, or discuss your application with one of our engineers to determine the best solution for you.
Types Of Packing & Lantern Rings
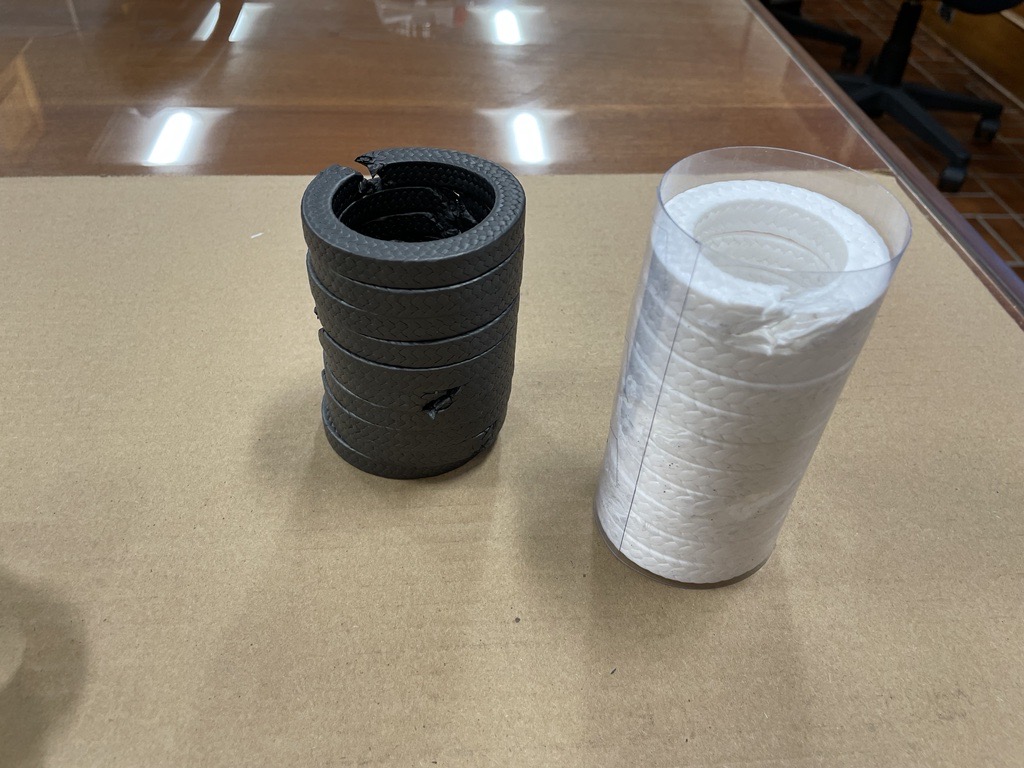
As mentioned previously, there are a number of packing materials, including:
- Graphite Packing: This is one of the most prevalent in the industry.
- Teflon Packing: This is often used on chemicals and food grade type services.
- Carbon Packing: This and other materials are used for high temperature.
- Polyimide Packing: Ideal for abrasive services.
- V-Groove Packing: This type of packing expands radially.
To determine the right packing material for your application, contact our Applications Engineering Team.
Packing may be supplied cut or uncut. When installing, it is very important that the cuts are not aligned but staggered and you use the correct number of rings per the pump’s instruction manual.
Lantern rings are designed to lubricate the packing from an external source. For example, if you are pumping chocolate you may use a lantern ring to lubricate it with a food grade oil or a pulp and paper plant may use the lantern ring to flush water. In cases cases where lantern rings are not used, the processed liquid will serve as the lubricant for the packing.
The Importance Of Breaking In Packing
When you are initially packing in a pump it’s very important to allow that packing to break in. At the start, the packing, sleeves and pump are all dry. To break-in, allow liquid to flow through the packing to lubricate it and then gradually tighten the packing gland to control the amount of leakage to 10 to 12 drips per minute.
Packed pumps will have a packing gland which fits into the stuffing box and compresses the packing to control leakage. With new packing, after installation of the gland there may be space between the stuffing box and the face of the gland. This allows room to tighten the packing as the pump is in service and begins to wear. When that packing gland is pressed flush against the housing it is time to replace the packing, and most likely the shaft sleeve as well.
When Is Packing Used Today?
There are many liquids out in the industry today that are very difficult to seal and packing is utilized. Liquids that benefit most from packing in pump applications include those that:
- Contain Abrasives
- Have slurry
- Solidify
- Have High Viscosity
- Have high temperature
Packing also has many applications other than pump seals. For example, many valve shafts contain packing to prevent leakage around the valve stem.
Mechanical Seals Basics
Mechanical seals are a widely used method of shaft sealing, and a common point of failure. Understanding how seals are selected and work will help you properly choose and maintain your seals to maximize their service-life.
How Mechanical Seals Work
A mechanical seal has two sealing areas:
- The Primary Sealing consists of a primary ring and a mating ring. The two rings are machined to be very flat, and ride on a thin fluid film to seal between the two faces. This is where most of the wear takes place and the most common location of failure.
- The Secondary Sealing consists of O-rings wedges, gaskets, labyrinths, and other areas not part of the seal faces.
In a properly applied seal, the combination of these two areas will seal liquid from the atmosphere. In most seals, because of the required fluid film there will be some leakage across the seal faces. This leakage is typically small enough that the fluid evaporates before it is visible. In the case of hazardous fluids, or where there are requirements for zero leakage, specially engineered seals and seal support systems are needed to prevent leakage.
Pusher vs Non-Pusher Seals
There are two basic options for mechanical seals:
- Pusher Seals have springs to hold the faces in contact, and dynamic O-ring to make sure the seal faces are held in contact with proper loading. Pusher seals can be susceptible to clogging.
- Non-Pusher Seals have a static O-ring. The most common version of a non-pusher seal is the Bellows type seal. The bellows can be self-cleaning.
Selection of Mechanical Seals
To correctly choose a mechanical seal for service, your application engineer will need to know:
- What are you pumping?*
- What is the temperature of the liquid?
- What is the vapor pressure and viscosity?
- Are there abrasives or solids?
- What is the operating pressure? Both the suction and discharge pressure.
- What is the model of the pump, or other rotating equipment?*
*Note: Mechanical seals can be used with many machines other than pumps. Geiger routinely provides mechanical seals for mixers, agitators, blowers, vacuum pumps, and more.
With this information, our application engineers can assist you with selection of a seal for your particular equipment and application.
Material Options For Mechanical Seals
There are a number of material options available for mechanical seals. The most common seal faces are made of carbon face or a hardened hard face like tungsten carbide or silicon carbide. The most common material is 316 stainless steel and the O-ring materials include common elastomers such as Buna-n, Viton, Aflas, and Kalrez. Application engineers can assist you in the selection of materials for your application.
What Are Retrofits?
Rotating equipment’s seals can often be retrofitted from one seal or style of shaft seal to another. For example, replacing packing with an o-pro or mechanical seal can reduce leakage or make the seal easier to maintain. To select a replacement seal, several measurements will be needed, including:
- Shaft size or shaft sleeve diameter
- Available room in the stuffing box to fit a mechanical seal
- Distance to the first obstruction
Note, many types of pumps can accept industry standard sizes of seals. In many cases, the model number of pump is all that is needed to confirm a new seal will fit the old pump.
Component vs Cartridge Seals
Mechanical seals are sold in two ways:
- Component Seals consist of all the major components you need within a mechanical seal, such as the rotating element, a static mating ring and gland. These components come as parts and must be properly assembled in the field.
- Cartridge Seals come as a fully assembled unit. They are significantly easier to install than component seals.
Proper installation is key to maximizing seal life. Faces must be clean, undamaged, properly aligned, and correctly compressed. Component seals are less expensive than cartridge seals, but are much more difficult to properly install than cartridge seals; for this reason we recommend cartridge seals whenever possible. Additionally, unlike a component seal, once a cartridge seal has completed much of its useful life, it can often be repaired at about half the cost of a new seal.
Curious about the installation process? Request our 1-hour video demonstration of how to install.
Improving Seal Reliability
Seal failures are a common source of frustration for pump users, but with some attention and expert collaboration great improvements in time between failure can be achieved. Geiger’s team of engineers and technicians is ready to help. To get started, contact us here.
80% of premature failures are due to either preventable mechanical or operational issues. Read on to learn how to maximize time between failure by assuring a sound installation and good operational practices, and what else you can do to address seals that are experiencing frequent failures.
Protect Mechanical Seals with Proper Installation
Installation in a pump with other mechanical issues is a major contributor to premature seal failure. When installing a seal, you should additional consider:
- If the bearings are in good condition
- If the shaft is straight – check runout
- If seal chamber or stuffing box areas are flat enough to seal a gasket against
Once these are checked, the next consideration is pump and driver alignment. Misalignment causes many pump seals to fail, so it is an important check between the output shaft of your pump and output shaft of your drive mechanism. If you do not have the ability to check alignment, your pump supplier should be able to provide this service.
Impeller balance should also be considered. An unbalanced impeller causes cyclic shaft deflection which can quickly contribute to seal failure. If you don’t have the equipment to check if your impeller is balanced, Geiger can provide impeller balancing services just contact our team to learn more.
Preventing Operational Seal Issues
Running a seal dry is the most common operational cause of seal failure. Common conditions resulting in dry run include:
- The supply tank running out of liquid
- The suction valve shut off, starving the pump
- A blockage in the line feeding the pump
- Vaporization of the liquid at the seal faces
- A closed discharge valve, deadheading the pump (while not technically dry run, causes a rapid buildup of heat, easily damaging the seal)
- Some seals are more resilient to running dry than others. If dry run conditions are not preventable, Geiger can recommend solutions. Read about one such case study using diamond faced seals here.
Pump operators should also be aware of where their pump is operating on its performance curve. All centrifugal pumps will have a “Best Efficiency Point” or BEP. At BEP, several key mechanical forces in the pump balance each other reducing shaft deflection during operation and resulting in maximum seal reliability, in addition to achieving the lowest energy usage. Knowledge of the pump’s curve allows adjustment of operation so the pump is not running very far out or back on the curve, as close to BEP as possible.
Proper Piping Plan
Seal piping plans are designed to provide a clean cool environment for the mechanical seal and the seal chamber. They may use heat exchangers, separators, flushing or quenching, and many other mechanisms, depending on the type of seal and operating environment. Revising or adding the correct seal plan can often significantly extend seal life.
There are several standard piping plan variations on the market. John Crane offers a pocket piping plan guide with diagrams of piping plans for single seals, double seals, pressurized, non-pressurized, gas barrier seals, etc. Geiger can aid in selecting an appropriate seal plan for your pump application. For direction on choosing the right piping plan, contact our team.
Proper maintenance of seal piping plans is important to maintaining their effectiveness. Examples include:
- Cleaning strainers
- Replacing worn orifice plates
- Cleaning or replacing tubing coming from suction or discharge.
- Maintaining reservoirs for double seals and gas seals
View The John Crane Mechanical Seal Piping Plan
Bad Actors
A bad actor is a seal that is experiencing frequent failures. While it can seem daunting, there are ways to improve bad actors and increase the mean time between failure (MBTF).
The first step to approaching a bad actor is to perform a failure analysis. This can be as simple as disassembling the seal to look at the internal components. Many times, this will expose issues such as:
- O-rings that were attacked, swollen, nicked, or missing.
- Seal faces with chips, nicks, or wear patterns due to pumping an abrasive or running dry.
- Uneven wear tracks signaling misalignment or non-perpendicularity between the seal and the stuffing box
If an issue is not quickly apparent to the naked eye, then a more in-depth failure analysis is needed. This evaluation is usually performed by a laboratory and results in a detailed service report with pictures, and a final recommendation.
Common recommendations include:
- Upgrading the seal faces or O-rings
- Changing the seal material to a higher alloy
- Changing the whole seal design
- Changing the piping plan, etc.
Finally, most seal manufacturers today offer repair programs available through the distributor. These programs allow return of the seal to the distributor for a repair quote, often 40-50% less than the cost of a new seal. Additionally, seal repair can happen in about half the time generally needed to get in a new seal with turnaround in urgent situations often available in only a few days.
Innovative Solutions for Shaft Sealing
Selecting the correct shaft seal depends on a wide variety of factors, including the fluid, type of plant, regulations, and customer preference. Careful selection of sealing equipment allows plants to reduce their environmental impact, increase efficiency and reliability of their equipment, and reduce costs. Read on to learn about innovative, problem-solving technologies now available for shaft sealing.
Diamond Face Seals
Diamond face seals should be considered in applications that experience continuous failures due to abrasive particles getting in the liquid, vapor pressure margin being less than ideal, and frequent dry running. In these applications, diamond face seals have proven to extend seal life dramatically. They are available on all standard types single and double cartridge seals.
Split Seals
Split seals are mechanical seals designed with a split to allow installation in two halves joined around the shaft, rather than the traditional seal assembly slid over the shaft. Split seals allow the installation of mechanical seals on large shafts which previously would have been impractical for any seal other than packing, and can significantly reduce time required to maintain large mechanical seals.
O-Pro Seal
Viking’s O-Pro seal was designed specifically for the Viking pump and chocolate applications and can now be found on a wide variety of applications. Most food plants traditionally use packing, resulting in many pumps leaking chocolate or syrup onto plant floors. The O-Pro seal was specifically designed to provide superior sealing than packing on applications that are not appropriate for mechanical seals.
The O-Pro also eliminates the need for a bracket bushing, which is a common area of seizure in a food processing type of pump. Additionally, with installations like a cartridge seal, the O-Pro can be installed very easily, and is a suitable retrofit for many packed pumps. O-Pro uses a reservoir of food grade grease inside a series of O-rings, keeping the pumped fluid out of that area, eliminating leakage. Maintenance consists of occasional re-greasing of the O-Pro barrier seal.
While originally developed for the chocolate industry, the O-Pro has expanded into many other markets including asphalt, corn syrups, starches and more. To learn if the O-Pro is right for your application, contact our team.
Double Seals
A double seal is two seals operating at the same time on the same shaft. This is advantageous because leakage of the process fluid to the atmosphere is virtually eliminated, however, it also requires a second seal that needs to be lubricated.
There are two types of double seals:
- Wet Seal requires a barrier fluid.
- Gas Seal uses nitrogen or air.
When using a Wet Seal, either a pressurized or unpressurized barrier fluid is required. It is important to note, a pressurized barrier fluid will leak into your process in the event of a seal failure while an unpressurized barrier fluid would allow processed fluid to leak into the reservoir. In either case, the barrier fluid or gas should be carefully selected. Double seals can also be used in situations where a viscous liquid must be kept out of the seal faces.
The alternative to choosing a Wet Seal is the Gas Seal. A Gas Seal is used in instances where you can’t have any contamination of your processed fluid, but you also don’t want any leakage to the atmosphere. In terms of application, many chemical plants elect to use gas seals. Lift-off, dry running seals are also available.
A Gas Seal uses either a nitrogen supply or an air supply to create a lift off condition in the seal faces. The seal faces on a gas seal are very different from your typical mechanical seal; they have very fine spiral grooves etched into the seal face. These spiral grooves allow the nitrogen or air to pass through and create the necessary lift off condition. There are some limitations to the gas seal, for example there will be a minimum shaft speed for the seal to maintain the liftoff condition. Your seal supplier can advise which conditions need to be met to have a successful seal. Please contact our team for more information.
Double seals (either Wet or Gas) are not only reserved for pumps; they can also be used on agitators and mixers. Generally, the seals on agitators and mixers are installed at the very top entry of the vessel and will therefore always need to be dry running to seal vapors in the vessel. Agitator seals generally run at very low speeds, some as low as 10, 20 or 30 RPM. This generates less heat at the seal faces.
Have Questions About Mechanical Shaft Seals?
Our team is ready to recommend solutions for your shaft sealing challenges. You can learn more about our offering of Mechanical Seals here or contact our team to discuss your unique application.